
Production of microfibrillated cellulose
To boost your products by releasing microfibrils from the fibre wall
- To produce microfibrillated cellulose (MFC) from lignocellulosic fibres, at laboratory scale or at pilot scale
- To characterise the MFC and to evaluate their potential as reinforcing agent or as barrier for your papers and boards
- To innovate for improving your product quality
Generate Value...
Cellulose is the most abundant natural, renewable, biodegradable, recyclable polymer on Earth. Lignocellulosic materials, such as wood, are composed of fibres with walls consisting of microfibrils of cellulose, which have exceptional mechanical properties. These microfibrils of cellulose can be used to:
- Improve the barrier properties of packaging papers and boards
- Enhance the film-forming capabilities of numerous products, such as varnishes
- Strengthen papers and boards
- Support specific molecules with specific properties (anti-bacterial, etc.)
- Develop new cellulosic products (LED, battery, etc.)
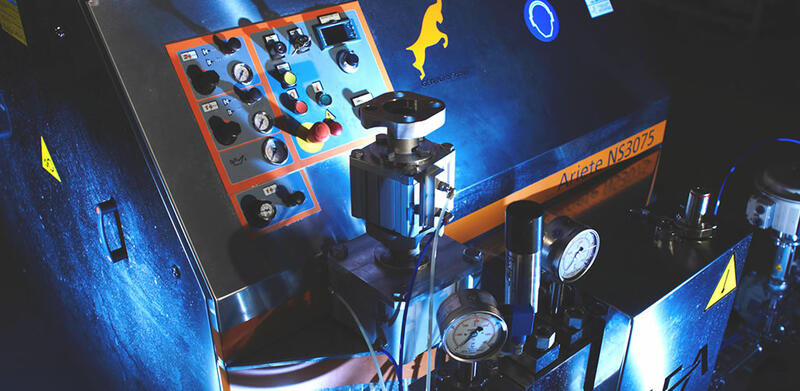
The Young’s modulus of microfibrillated cellulose is comparable to the steel one, and adding them in a small percentage can improve the mechanical properties of papers and boards by more than 50%. When functionalised, they can enhance products with new properties.
Context and performance
The microfibrillated cellulose production process is based on releasing the elements constituting the secondary wall of lignocellulosic fibres using mechanical means combined with enzyme or chemical pre-treatment. The lignocellulosic fibres used may be bleached or unbleached chemical pulps or mechanical pulps produced using wood or annual plants, recycled fibres...
From your raw material, microfibrillated cellulose can be extracted using a protocol established according to the targeted MFC quality. It will be based on a mechano-enzymatic pre-treatment or a TEMPO oxidation followed by high-pressure homogenisation.
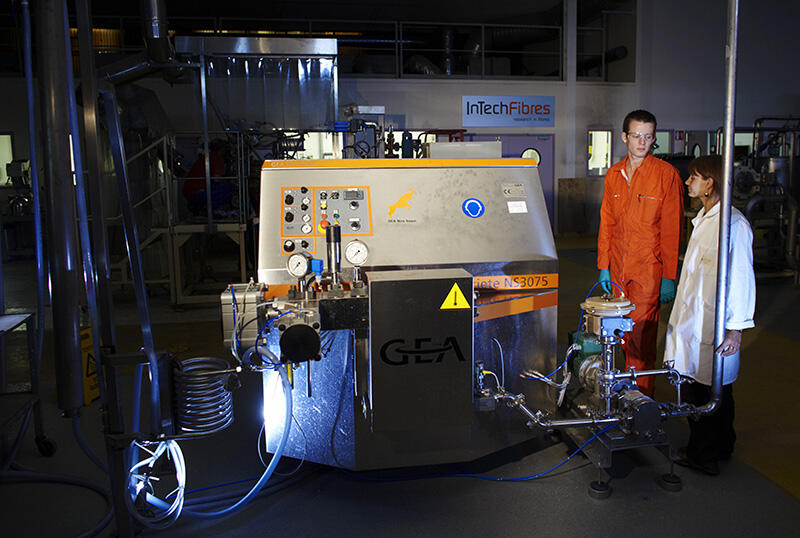
Content of services
- Production of native MFC
From a batch of lignocellulosic fibres of approx. 5 kg, an enzymatic treatment followed by an intensive refining is carried out to fibrillate and cut the fibres. This hyper-refined pulp is homogenised at very high pressure (1500 bar) in several passes to produce MFC. - Production of oxidised MFC
From a batch of lignocellulosic fibres of approx. 300 g, a TEMPO mediated oxidation allows introducing carboxyl groups on the cellulose and facilitating the microfibrils separation. This oxidised pulp is then homogenised to produced MFC. Three homogenisers are available to produce batches from 50 g to 30 kg. MFC suspensions have a gel-like structure with a consistency of 2 to 4%. - Characterisation of MFC
The gels produced are characterised by:
-Their viscosity,
- Their homogeneity (optical microscopy),
- The analysis of residual coarse elements (MorFi analyser)
- The size of microfibrils (electronic microscopy). The reinforcing effect of MFC can be studied on standard and dynamic handsheets.
MFC films can be produced and characterised in terms of strength, transparency and barrier properties.
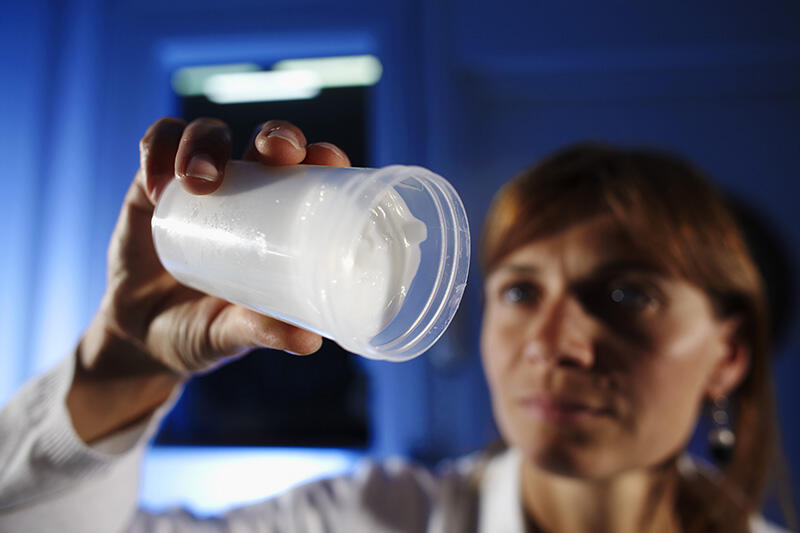
Deliverables
- Supply of MFC gels in required quantity
- Production and characterisation report on the batches produced.