
Development of lignocellulosic foams
A bio-based and recyclable alternative to plastic foams
- Design bio-based, recyclable foams in the paper-board sector
- Identify suitable formulations for achieving the desired properties
- Characterise foams and compare them with existing products
Generate Value...
The demand for cellular materials is constantly growing in a wide variety of fields of application (building construction, transport, packaging, consumer goods, etc.). The global market in 2018 was worth 97.55 billion euros and there were considerable prospects for growth. These foams, already widely used on account of their cushioning, insulating and soundproofing properties, are now spreading to high-tech fields (aerospace, biomedical, filtration) because they are much lighter than alternative materials. However, given the current concerns over sustainable development, it is becoming increasingly necessary to find bio-based and biodegradable alternatives to synthetic plastic foams. Solutions have already been proposed, but their use is limited by various factors (price, performance level, recyclability, competition with food resources).
Lignocellulosic materials are an excellent, competitive alternative to plastics: they are renewable, biodegradable, readily available and cheap.
Drawing on its expertise in the use of foams for deinking, the CTP has initiated research and development into lignocellulosic foams for a wide range of applications.
Context and performance
Lignocellulosic foams can be developed in a variety of ways, one of which is by introducing air in a controlled manner into a fibre suspension to create a liquid foam.
The foam’s structure is then consolidated by eliminating the water through drainage and evaporation.
The characteristics of the liquid foam, adjusted by means of the fibre suspension formulation, are essential for consolidating and stabilising the material.
The formulation also plays a key role in determining the final properties of the material and its compliance with the specifications defined for different applications.
The CTP has acquired facilities for producing liquid foams, transforming them into solid foams and characterising them.
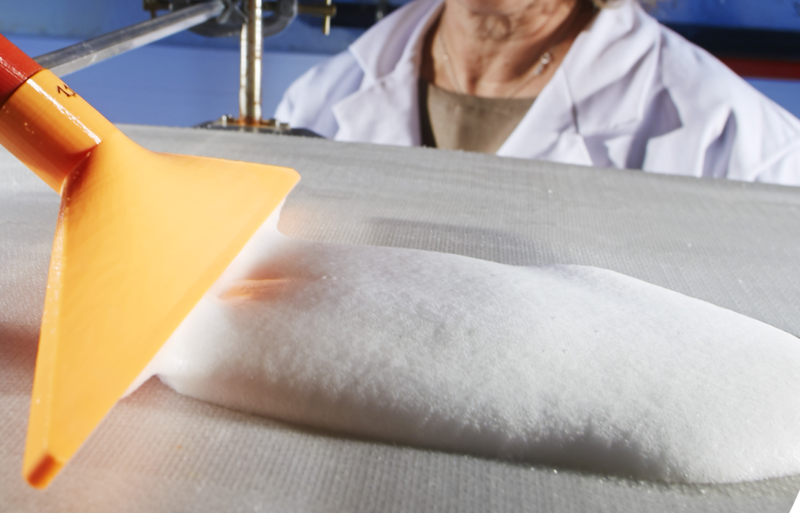
Foam generator
Content of services
The CTP’s facilities, methodology and expertise gained with three-phase media (gases, water, particles) are available for developing new lignocellulosic foams as a replacement for the synthetic polymer foams used in the packaging, medical and other sectors. One example is the use of liquid foams as a vehicle for transporting particles to be deposited on substrates.
Depending on the application involved, the study may include:
- selecting the appropriate foam production system;
- defining the parameters for obtaining a liquid foam with optimal stability for shaping;
- optimising the foam formulation and producing representative samples;
- characterising the foams obtained and checking their compliance with the specifications
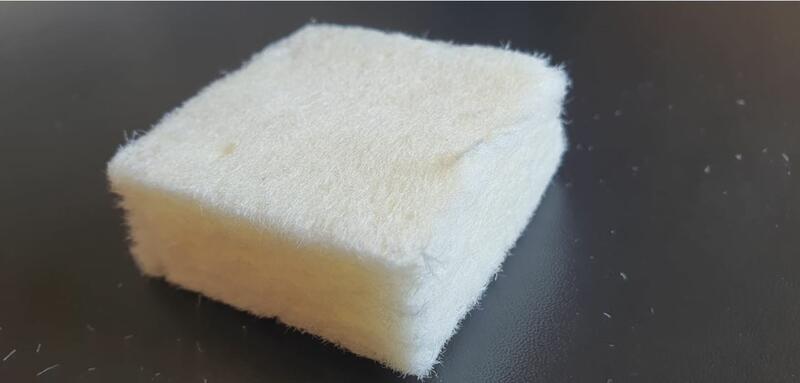
Dry cellulose foam
Delivrables
- Study report, giving details of the materials and methods used, the results obtained and both general and specific conclusions/recommendations.
- Samples.